
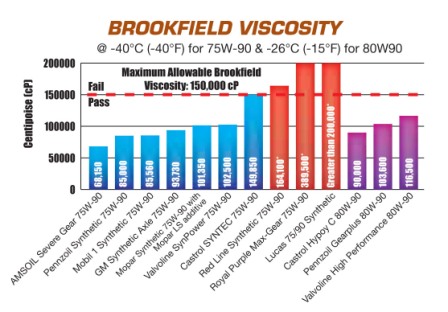
A variable temperature glue gun gives you the freedom to be able to make these adjustments while dispensing. The dynamic viscosity (Greek letter eta) is normally given in millipascal-seconds (mPas) and is usually determined by using a rotary viscometer. Higher temperatures will lower the viscosity and lower temperature will increase it. Hot melt viscosity can also be tweaked by adjusting the temperature at which the adhesive is being dispensed. Reiner and Phillippoff suggested the following formula: dUx dy ( 1 + 0 1 + ( xy s)2)xy. The viscosity index (VI), which is calculated with. The higher viscosity is more dominate at low shear stress. For instance, some product assembly or gap filling formulations may require a thicker hot melt where packaging may use a lower viscosity (thinner) material. Temperature differences of, for example, 10C do not lead to identical number jumps in viscosity changes. Urethane and epoxy resins with viscosities ranging from <100cP to 1,000cP are ideal for most generic casting applications. Refer to our viscosity comparison chart here. Some products are formulated to run thicker or thinner depending on how they are being used. Viscosity numbers range from 1 (water) to millions of centipoise (cP) or pascal seconds (Pa.s), 1cP 0.001 Pa.s. There are a number of factors that affect the viscosity of hot melt. We have created a chart below to help you get an idea the viscosity of everyday items in centipoise. Viscosity is not an easy concept to comprehend, but is an essential factor for adhesives. Viscosity classification systems provide a uniform and common basis for designating lubricants. Since thicker products are less flowable they will fill in a larger gap if necessary. The higher the number of cps the thicker the product.
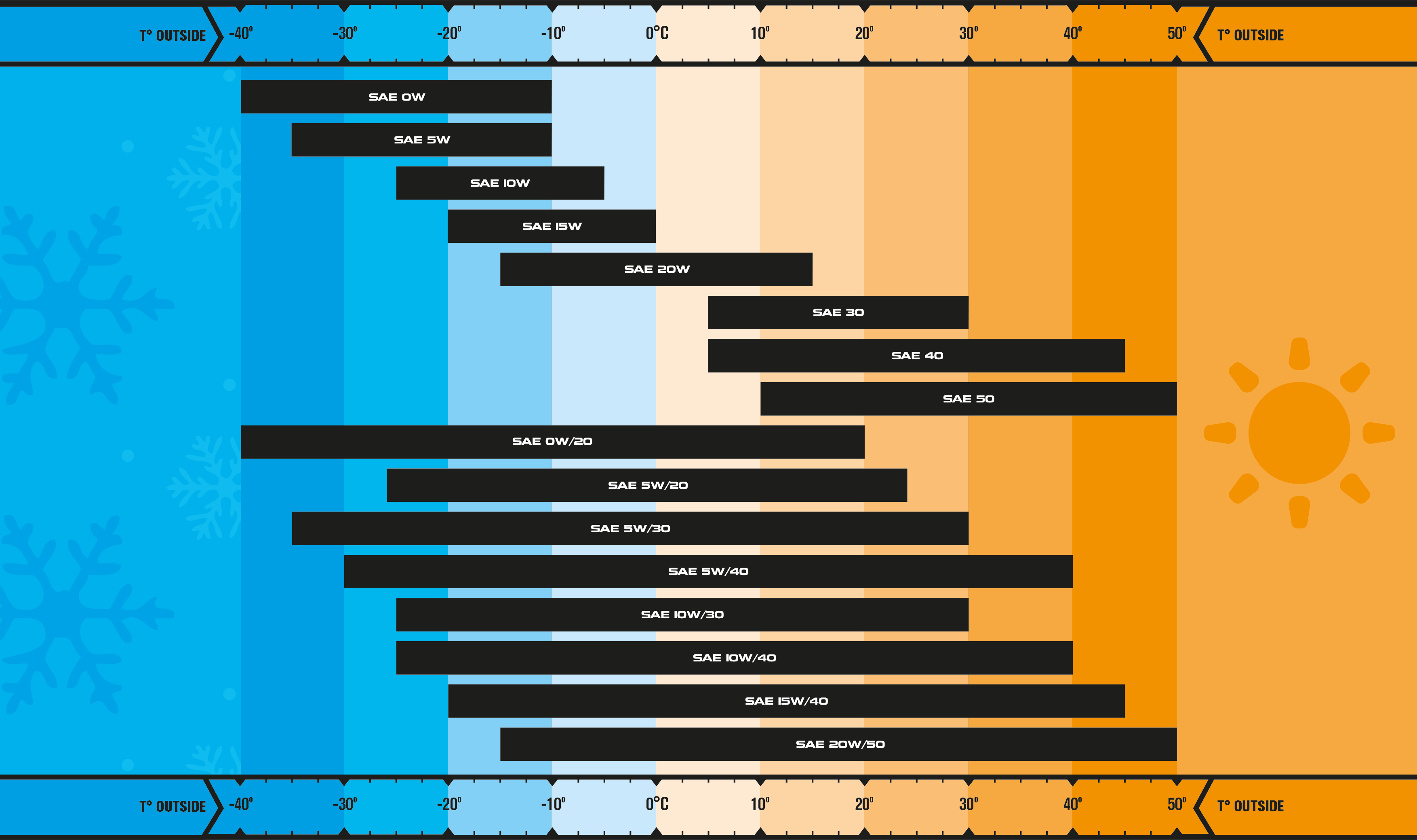
The measure of this fluid "thickness" is expressed by centipoise values.
#Viscosity comparison chart iso#
Lubricants of a given ASTM or BSI grade are slightly more viscous than lubricants of the corresponding ISO grade.Viscosity is the resistance of a fluid to flow generally through a specific orifice. Drag Coefficient - The drag coefficient quantifies the drag or resistance of an object in a fluid environment. Viscosity grade numbers of the ISO are the same as those of ASTM (The American Society of Testing and Materials) and BSI (British Standards Institution), with the difference that the viscosities for the ISO grades are measured at 40 ☌, while those of the ASTM and BSI are measured at 100 ☏ (37.8 ☌). Gravity - Viscosity at 20☌/68☏ and 50☌/122☏ for more than 120 crudes is shown as function of specific gravity15☌/60☏. Viscosity table/chart as per ISO 3448 for industrial fluids. This comparative viscosity chart shows the relationship between the various viscosity grading systems (viscosities are related horizontally). The ISO system is primarily used for hydraulic oil, industrial oils, such as turbine oils, compressor oils and others. ISO VG are based on kinematic viscosity of the lube oil/fluid at 40☌. ISO viscosity classification system or ISO Viscosity grades also called ISO VG contains 18 viscosity grades. The force necessary to move a plane of area A past another in a fluid is given by Equation 2.6. Lubricant viscosity performs a prime role against friction and wear. The moving plane has area A and requires force F to overcome the fluid’s internal resistance. Settled in 1975 by a joint committee of International Standards Organization (ISO), American Society for Testing and Materials (ASTM), Society for Tribologists and Lubrication Engineers (STLE), British Standards Institute (BSI), and Deutsches Institute for Normung (DIN). A viscosity grades classification or standard known as the ISO VG (International Standards Organization Viscosity Grade). For engine oil check SAE J300 and SAE J306 for gear oils. ISO-VG (Viscosity Grade) classes apply only for industrial lubricating oils. Industrial fluids kinematic viscosity according to ISO 3448, DIN 51519
